3DスキャナーでPDCAを回す!清水建設が開発したトンネル発破システムの節約効果
爆薬によって発破しながら掘っていく山岳トンネル工事では、計画断面より小さくなるマイナス誤差は許されません。かといって、計画断面より外側に「余掘り」を大きくして掘ればいいかというと、今度はコスト面の理由で許されません。
発破後の「ずり」と呼ばれる岩石の搬出や処理、計画に合わせるためのコンクリート打設、そして発破に使う爆薬など、すべてのコストが余掘りの分だけ大きくなってしまうからです。
そのため、トンネル工事を手がける建設会社は、いかに「余掘り」を小さくするかにしのぎを削っています。
そこで清水建設は、サンドビック株式会社SMRTカンパニー(本社:横浜市港北区)と、余掘り量低減システム「ブラストマスタ」を共同開発し、実用化しました。
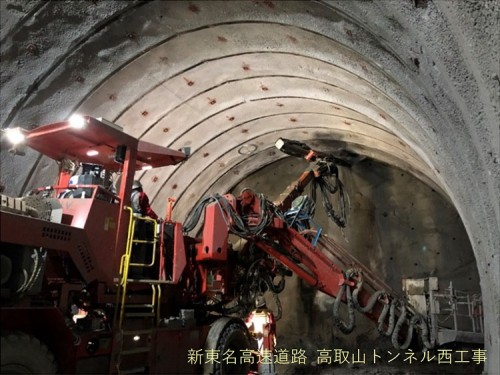
ブラストマスタを導入した新東名高速道路「高取山トンネル西工事」の現場(以下の写真、資料:清水建設)
余掘りを少なくするために重要なのは、「発破パターン」と呼ばれる爆薬を装填(そうてん)する穴の位置と角度の調整です。
ブラストマスタは、ある発破パターンで発破した後、切り羽(掘削最前面)の空間形状を、
ナ、ナ、ナ、ナント、
3Dスキャナー搭載車両
で計測するのです。(清水建設のプレスリリースはこちら)
こうして発破後の余掘り量を精密に把握した後、余掘りに最も影響を与える切り羽外周部の穴の位置と角度の最適値を求め、掘削機に入力している発破パターンを自動更新します。この過程で所要時間はわずか3分しかかかりません。
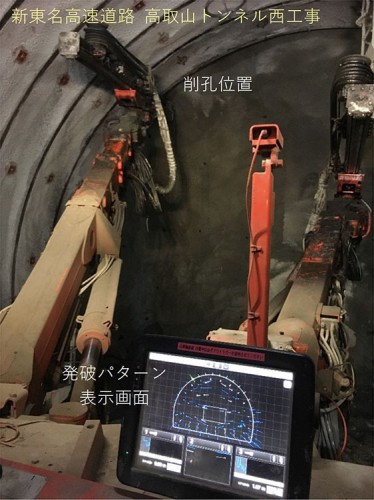
手前のタブレットの画面には発破パターンが表示されている
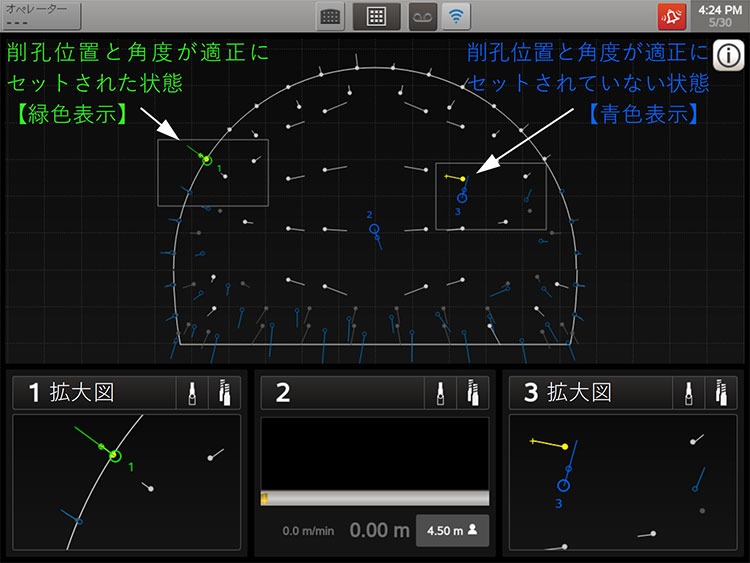
画面の拡大図。掘削位置や角度が設定データと離れている場合は青色で表示され、精度よくセットされた場合は緑色で表示される
これまでも3Dスキャナーで余掘りを計測する試みは行われてきましたが、システマチックではなく、発破パターンの更新にも時間がかかったので発破のたびにパターンを修正することはできませんでした。
その点、ブラストマスタは、発破パターンの作成→削孔→3Dスキャナーによる計測→削孔位置・角度の調整されたデータの削孔機への転送という一連の作業が自動化されており、
発破のPDCA
が、発破のたびに回る仕組みになっているのです。
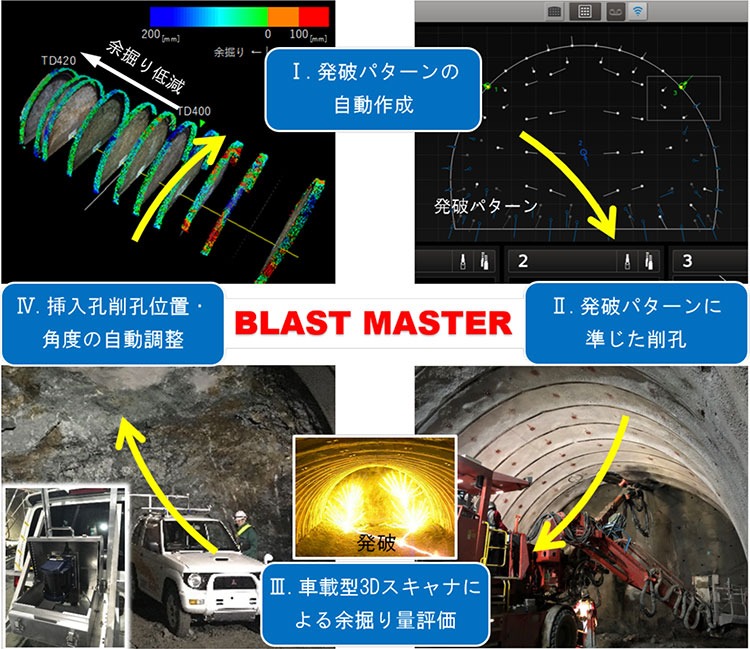
システム概要図。発破パターンの自動作成(Plan)→削孔(Do)→余掘り計測(Check)→削孔位置と角度の自動調整(Action)がシステム化されている
上の図の左上にある図を見ても、PDCAが回るたびに余掘りが小さくなっている様子がうかがえますね。
このシステムが初導入された新東名高速道路高取山トンネル西工事では、余掘り量を既存システム比で40%も減らすことができました。PDCAによる節約効果はあなどれませんね。
一般にP(Plan)やC(Check)はデータの世界、D(Do)とA(Action)はリアルな世界で行われることが多いですので、リアルとデータが測量機器や自動化機器などで自動的につながるようになれば、PDCAによる施工の改善は、ますますスムーズに行えるようになりそうです。
最終更新:2019/11/2018:08